Advanced Holders for Cutting Tools, Diamond Tools, CBN Tools, and Laser Optics
By:Admin
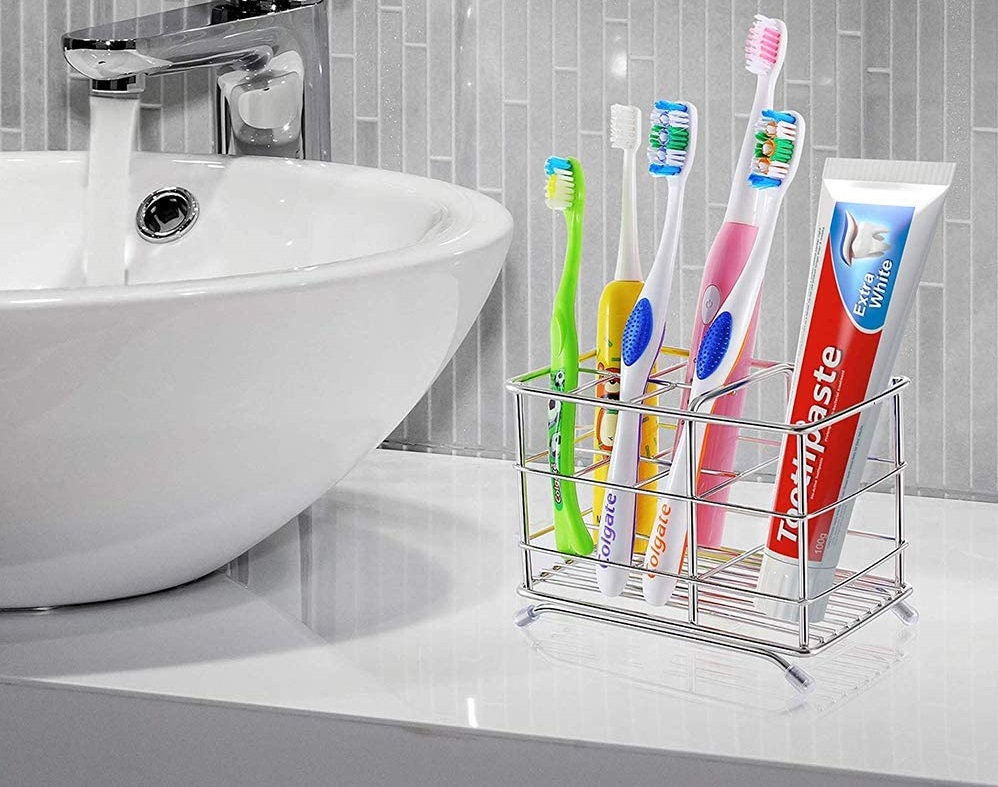
In the realm of cutting tools, there is an ever-growing demand for increased efficiency and precision. Industries across the board, from automotive to aerospace, are constantly seeking innovative solutions to optimize their manufacturing processes. This pursuit has led to the development of diamond tool holders, a game-changing technology that has revolutionized industrial cutting.
Diamond tool holders are essential components in cutting machinery, serving as the interface between the machine and the cutting tool. They are meticulously designed to provide stability, accuracy, and durability. The incorporation of diamonds in the tool holder material adds an extra layer of robustness, making it much more resistant to wear and tear compared to traditional tool holders.
One of the key advantages of diamond tool holders is their exceptional hardness. Diamonds are known to be one of the hardest substances on Earth, surpassing all other materials commonly used in tool holders. This unique property allows diamond tool holders to withstand the extreme forces and temperatures experienced during cutting operations, resulting in a longer tool life. As a result, manufacturers can significantly reduce downtime and tool changeovers, leading to enhanced productivity and cost savings.
Another noteworthy characteristic of diamond tool holders is their superior thermal conductivity. Heat generation is an inherent challenge in cutting processes, as excessive heat can negatively impact the tool's performance and lead to premature failure. However, diamond tool holders effectively dissipate heat due to their excellent thermal conductivity, ensuring the tool remains at an optimal temperature. This feature is particularly beneficial in high-speed cutting applications where heat buildup is a common concern.
Furthermore, diamond tool holders minimize vibrations during machining operations. Vibrations can have a detrimental effect on the quality and precision of the final product. The inherent stiffness and rigidity of diamond give these tool holders remarkable dampening capabilities, reducing vibrations to negligible levels. By mitigating vibrations, diamond tool holders contribute to smoother cutting actions and improved surface finishes, meeting the stringent quality requirements of various industries.
Diamond tool holders also excel in their ability to maintain dimensional accuracy. Precision is a critical factor in industries that demand tight tolerance in their manufacturing processes. Diamond's exceptional hardness and wear resistance ensure that the tool holder maintains its shape and size over extended periods of use. This consistent dimensional stability translates to consistent, high-quality products and eliminates the need for frequent adjustments or replacements.
Moreover, the introduction of diamond tool holders has significantly expanded the scope of cutting tool applications. Diamond tool holders are compatible with a wide range of cutting tools, including both diamond and CBN (cubic boron nitride) tools. This versatility allows users to select the most suitable cutting tool for their specific application, optimizing performance and achieving desired outcomes. Industries such as automotive, aerospace, and medical device manufacturing have greatly benefited from this increased flexibility in tooling options.
In conclusion, diamond tool holders have transformed the industrial cutting landscape. Their exceptional hardness, thermal conductivity, and dampening capabilities make them a superior choice for precise, efficient, and reliable cutting operations. By choosing diamond tool holders, manufacturers can improve productivity, achieve consistent and high-quality results, reduce downtime, and ultimately save costs. As the cutting tool industry continues to evolve, diamond tool holders remain at the forefront of innovation, empowering industries to push the boundaries of what is possible in the realm of cutting technology.
Company News & Blog
High-Quality and Reliable Universal Diamond Cutting Disc 125x22.23mm - Professional Power Tools
article on the importance and benefits of using high-quality diamond cutting discs in various industries.As technology advances and new materials are developed, the need for precise and efficient cutting tools becomes increasingly important. In many industries, the use of cutting discs is crucial for producing high-quality products and completing tasks with precision and accuracy. With so many different types of cutting discs available on the market, it can be overwhelming to choose the right one for your specific needs.One type of cutting disc that has gained popularity in recent years is the diamond cutting disc. Diamond cutting discs are quickly becoming the standard for professionals in a wide variety of industries due to their exceptional strength, durability, and precision. These discs are made with industrial diamonds that are bonded to a metal or resin matrix, which provides a superior cutting edge that can handle tough materials like concrete, metal, glass, and ceramic tiles.One of the key features of diamond cutting discs is their versatility. Thanks to their durable composition, diamond cutting discs can cut through a wide range of materials, making them a go-to tool for professionals in a variety of industries. This versatility means that contractors and tradespeople can have a single cutting disc to handle various cutting needs, which can save them both time and money.Another benefit of diamond cutting discs is their long lifespan. With regular use and proper maintenance, diamond cutting discs can last significantly longer than traditional cutting discs. This is because the industrial diamonds used to make diamond cutting discs are incredibly hard and resilient, making them more resistant to wear and tear. Additionally, the bond that holds the diamonds in place is designed to withstand high temperatures and stress, further extending the lifespan of the disc.Aside from their durability, diamond cutting discs also offer exceptional cutting speed and precision. Because the industrial diamonds are much harder and sharper than traditional cutting materials like aluminum oxide or silicon carbide, they can cut through materials much faster, with less force required. This faster cutting speed not only increases efficiency on the job but also leads to a smoother finish with fewer burrs or jagged edges.When it comes to choosing a diamond cutting disc, it's crucial to consider factors like blade size, material composition, and intended use. For example, the Metabo diamond cutting disk 125x22.23mm, "UP", Universal "professional" (628559000) is designed to be a high-quality, reliable, and durable option for professionals in various industries. Its 125mm diameter makes it suitable for cutting a wide range of materials, while its universal "professional" design means that it can handle the toughest applications with ease. As a product known for its exceptional quality and performance in the industry, using it can ensure optimal results every time.In conclusion, there are significant benefits to using high-quality diamond cutting discs in various industries, including their versatility, long lifespan, and exceptional speed and precision. Although the initial cost of diamond cutting discs may be higher than traditional cutting discs, the superior performance and longevity make them a worthwhile investment in the long run. By choosing the right diamond cutting disc for your specific needs, you can ensure optimal results and save both time and money in the process.
Augusta Metal Recycling Facility Receives Green Light for $760M Bond Authorization
Title: Sustainable Industrial Growth: Metal Secondary Recycling Facility Secures Bonds ApprovalIntroduction (approx. 100 words)In recent news, an Augusta metal plant has been granted authorization for $760 million in bonds, marking a significant step towards establishing a state-of-the-art metal recycling and secondary smelting facility. However, it faced criticism from the Savannah Riverkeeper regarding air permit issuance. In this blog, we will dive deep into the implications of this development, shedding light on the potential of metal secondary recycling, and highlighting the positive impact it can have on sustainability and the environment.Understanding Metal Secondary Recycling (approx. 250 words)Metal recycling is a crucial aspect of the modern industrial landscape, contributing to both environmental conservation and economic growth. Secondary smelting facilities play a pivotal role in the recycling process by converting scrap metal into reusable material, reducing the industry's reliance on virgin metal production. By doing so, these facilities contribute to a circular economy while minimizing waste generation.Facility Overview and Importance (approx. 200 words)The recently authorized metal recycling and secondary smelting facility in Augusta will serve as a beacon of sustainable industrialization, demonstrating the tremendous potential of such operations. With an investment of $340 million, the facility aims to refine metal scraps through an innovative secondary smelting process, effectively minimizing the environmental footprint associated with traditional metal production.Benefits of Metal Secondary Recycling (approx. 300 words)1. Environmental Impact: Metal recycling significantly reduces energy consumption, greenhouse gas emissions, and the extraction of natural resources. By utilizing secondary smelting, this facility will effectively minimize carbon emissions, deforestation, and water pollution, while preserving valuable natural resources for future generations.2. Economic Growth: The establishment of such a facility generates employment opportunities, stimulating local economies and ensuring long-term sustainable growth. Additionally, increased recycling rates not only reduce waste management costs but also provide a reliable and affordable source of raw materials for various industries.3. Energy Conservation: Secondary smelting facilities contribute to energy conservation by requiring significantly less energy compared to primary metal production. By utilizing advanced technological processes and efficient energy management systems, this facility will play a crucial role in mitigating the energy crisis and advancing sustainable development.4. Resource Conservation: Metal recycling and secondary smelting mitigate the need for extracting and processing new ores. This, in turn, helps preserve our finite natural resources, lessens environmental degradation caused by mining activities, and reduces our dependence on foreign sources of raw materials.Conclusion (approx. 150 words)The authorization of $760 million in bonds for the Augusta metal plant signifies a promising step towards establishing a sustainable metal recycling and secondary smelting facility. By embracing advanced technologies and innovative practices, secondary smelting operations demonstrate the potential to achieve both environmental and economic sustainability. From reducing carbon emissions and conserving natural resources to supporting local economies and generating employment opportunities, such facilities can spearhead the transformation towards a circular economy.However, it is crucial to address the concerns raised by local communities, such as the Savannah Riverkeeper, regarding air permit issuance. Striking a balance between industrial growth and environmental stewardship is essential to ensure the success of projects like these. By incorporating robust environmental monitoring and control measures, the facility can further enhance its positive impact while maintaining harmony with its surroundings. Ultimately, the Augusta metal recycling and secondary smelting facility represent a remarkable effort towards a greener, more sustainable future.
Adopt DiaMEND Orange Diamond Restoration Screens to Repair Traffic Patterns and Stains on Concrete and Stone Floors
Title: Diamond Concrete Buffer Pads: The Ultimate Solution for Flooring RestorationIntroduction:Maintaining the pristine condition of concrete and stone floors is crucial for businesses and homeowners alike. Constant foot traffic, scratches, and stains can quickly mar the appearance of these surfaces, ultimately resulting in costly repairs. However, with the advent of advanced technology, solutions such as the DiaMEND Orange Diamond Concrete & Stone Restoration Screens have emerged to address these issues effectively. In this blog post, we will delve into the benefits of using these 400 Grit Orange Diamond Round Screens, which are compatible with existing floor buffers and auto scrubbers. Let's explore how Diamond Concrete Buffer Pads can revolutionize the way you restore your concrete and stone floors.1. Enhance Efficiency and Cost-effectiveness:The DiaMEND Orange Diamond Concrete & Stone Restoration Screens work wonders by tackling traffic patterns, scratches, and stains before they escalate into serious problems. By incorporating these screens into your floor maintenance routine, you'll not only save time but also mitigate the need for extensive repairs down the line, potentially saving you substantial costs.2. Premium Quality and Versatile Application:One crucial aspect of Diamond Concrete Buffer Pads is their exceptional quality. Manufactured with advanced orange diamond grit technology, these round screens provide remarkable durability and longevity. Whether you are dealing with uneven surfaces, deep stains, or light scratches, these pads prove to be an effective solution for all concrete and stone floors.3. Compatibility with Existing Floor Equipment:Integrating the DiaMEND Orange Diamond Concrete & Stone Restoration Screens into your existing floor buffers and auto scrubbers is seamless. This compatibility ensures that you don't need to invest in expensive new machinery, making it a cost-efficient and convenient solution for both commercial and residential use.4. Eco-friendly and Safe Usage:Conscious about the environment? Diamond Concrete Buffer Pads are the way to go! These pads are designed to be used with water, eliminating the need for harmful chemicals during the restoration process. With an eco-friendly approach, you can restore the beauty of your floors without causing harm to the environment or compromising on the safety of those who utilize the space.5. Unparalleled Performance:The 400 Grit Orange Diamond Round Screens exhibit remarkable performance, allowing you to achieve remarkable results. They effectively remove deep-seated stains, eliminate stubborn scratches, and restore the natural shine and smoothness of your surfaces. With consistent usage, your concrete and stone floors will regain their former glory, impressing visitors and enhancing the overall aesthetic appeal of your space.Conclusion:Investing in DiaMEND Orange Diamond Concrete & Stone Restoration Screens proves to be a game-changer in the realm of flooring restoration. By effectively addressing traffic patterns, scratches, and stains, these Diamond Concrete Buffer Pads save you from incurring costly repairs in the future. With their exceptional quality, compatibility with existing floor equipment, eco-friendly nature, and unparalleled performance, these 400 Grit Orange Diamond Round Screens become your go-to solution for concrete and stone floor maintenance. Embrace the future of flooring restoration and unlock the true potential of your surfaces with Diamond Concrete Buffer Pads!Keywords: Diamond Concrete Buffer Pad, DiaMEND Orange Diamond Concrete & Stone Restoration Screens, concrete floor restoration, stone floor restoration, floor maintenance, cost-effective solutions, versatile application, eco-friendly, compatibility with existing equipment, unparalleled performance.
12PCS Car Foam Drill Polishing Pad Kit for Easy Car Polishing and Waxing
The HMPLL 12PCS Car Foam Drill Polishing Pad Kit is a must-have for car enthusiasts looking to achieve a showroom-quality finish. This kit includes 12 different polishing pads, each designed to tackle specific aspects of the polishing process.Firstly, you will receive four waffle buffer polishing pads, perfect for removing swirls, scratches, and water spots from your car's paintwork. These pads are made from high-quality foam that is firm yet gentle on the surface. The waffle design allows for better absorption of polishing compounds, resulting in a smoother and more even finish.Additionally, you will also get four flat buffer polishing pads, ideal for applying wax or sealant to protect your car's paint from harmful UV rays and contaminants. These pads are designed to evenly distribute the product, ensuring maximum coverage and longevity of the protective layer.To further enhance the polishing process, the HMPLL kit includes one woolen buffer pad. This pad is perfect for removing stubborn oxidation or deep scratches. The thick and plush wool fibers effectively remove imperfections while also leaving a glossy finish.For the final touch, the kit includes one microfiber buffing pad. Microfiber is renowned for its superior polishing and buffing capabilities. This pad is great for removing any remaining residue and bringing out the ultimate shine on your car's surface.In terms of convenience, the HMPLL kit is equipped with a Velcro sucker. This attachment allows the pads to be easily secured onto a drill or polisher for efficient and effortless use. The Velcro design also ensures a tight and secure fit, preventing the pads from slipping or detaching during use.Furthermore, the branding on the kit is removable, allowing you to customize the appearance of your tools. Whether you prefer a clean and minimalistic look or want to add your own personal touch, the choice is yours.With the HMPLL 12PCS Car Foam Drill Polishing Pad Kit, you can say goodbye to tedious and time-consuming polishing processes. This comprehensive kit provides you with everything you need to achieve a professional-grade finish in the comfort of your own garage.Not only will your car's paintwork look visually stunning, but it will also be better protected against the elements. The waxing and buffing process creates a shield that repels water, dirt, and other contaminants, ensuring that your car stays cleaner for longer.In summary, the HMPLL 12PCS Car Foam Drill Polishing Pad Kit is a fantastic investment for anyone looking to elevate their car care routine. With a variety of pads and attachments included, you will have all the tools needed to achieve a flawless and long-lasting finish. Don't settle for anything less than perfection - choose the HMPLL Car Polishing and Buffing Kit today and enjoy the benefits of a showroom-quality shine.
Economical Wet Polishing Pads for Effective Granite Polishing
: Achieving a Perfect FinishGranite surfaces are remarkable in providing the perfect blend of style and durability. From kitchen countertops to floors, walls, and statues, granite is a popular material used in homes and commercial buildings. However, to ensure that your surfaces are always looking their best, you need to invest in a high-quality granite wet polisher. In this blog post, we will discuss achieving a perfect finish using a granite wet polisher.Why Use a Granite Wet Polisher?A wet polisher is an essential tool for polishing granite surfaces. As the name implies, a wet polisher works with water, which acts as a lubricant and cooling agent to prevent overheating of the granite. Wet polishing also helps to remove dust particles, ensuring a smoother and cleaner finish. A granite wet polisher removes scratches, brings out the natural shine of the stone, and eliminates any imperfections on the surface.Choosing the Right Polishing PadsWhen it comes to polishing granite, you need the right polishing pads. The Puma Economy Wet Polishing Pads are an excellent choice for achieving a perfect finish. These pads are designed to perform well at a great price, making them an economic option. Additionally, the Puma polishing system features exclusive Geo patterns that help displace and channel water during use, ensuring a smoother and more polished finish.The 7 Step Puma Polishing SystemThe 7 Step Puma polishing system includes seven different grits of polishing pads that help achieve a mirror-like polished surface. The grit progression starts from coarsest to finest, starting at 50, 100, 200, 400, 800, 1500, and ending with 3000. You need to follow each step of the polishing process with care, ensuring that you remove any scratches or rough spots before proceeding to the next step. Remember that each step prepares the surface for the next, so take time to complete each one before moving on.Steps to Achieving a Perfect Granite Polished SurfaceStep 1: Clean the SurfaceThe first step is to clean the granite surface thoroughly. Use a soft brush or vacuum to remove any dirt or debris on the surface.Step 2: Start with Coarse GritsAttach the 50-grit polishing pad to the granite wet polisher and start polishing the surface. Work in sections, keeping the pad flat and applying even pressure. Once the surface is smooth and free of scratches, move on to the next finer grit.Step 3: Progress to Finer GritsContinue working through the finer grits until you reach the 3000-grit polishing pad. At each stage, ensure that the surface is clean and free of scratches before moving on to the next grit.Step 4: Rinse the SurfaceOnce you've completed each stage, rinse the surface with water to remove any debris. Check that the surface is completely clean and free of scratches.Step 5: Apply Granite SealerAfter polishing, it's advisable to apply granite sealer to protect the surface from stains and water damage.Step 6: Buff the SurfaceUse a soft buffing pad on the granite wet polisher to buff the surface to a high shine. Use water to lubricate the surface and prevent heat damage.Step 7: Clean the Surface Once AgainFinally, clean the surface one last time to remove any buffing residue and leave the surface sparkling.ConclusionAchieving a perfect finish on granite surfaces requires patience, attention to detail, and the right equipment. By using a granite wet polisher with the correct polishing pads and following each step of the polishing process, you can achieve a mirror-like polished finish. The Puma Economy Wet Polishing Pads are an economic, quality option for achieving a perfect finish on granite surfaces. So the next time you're looking to polish granite surfaces, invest in quality tools, and you'll be proud of your finished product.
Versatile Diamond Polishing Pads for Granite, Marble, Stone, and More
Diamond Resin Dry Polishing Pads: Perfecting the Art of Stone PolishingDiamond polishing pads have become an indispensable tool in the field of stone polishing. With their ability to enhance the appearance of various types of surfaces such as granite, marble, engineered and natural stone, concrete, terrazzo, countertops, and floors, these pads have revolutionized the way we finish and beautify these materials. Among the many options available, Diamond Resin Dry Polishing Pads stand out as one of the best choices for achieving impeccable results. In this blog, we will explore the features, benefits, and applications of these remarkable pads that have taken the industry by storm.The first thing that sets Diamond Resin Dry Polishing Pads apart is their composition. Crafted using the finest quality of diamonds and resin, these pads are designed to deliver exceptional polishing performance. The diamonds embedded in the resin matrix provide the necessary cutting power, while the resin acts as a bonding agent, ensuring durability and longevity.One of the primary advantages of using Diamond Resin Dry Polishing Pads is their versatility. They can be used on a variety of surfaces, ranging from granite to marble, engineered and natural stone, concrete, terrazzo, countertops, and floors. This gives contractors and polishing professionals the flexibility to work on different projects without the need for multiple sets of pads. Whether you are polishing a kitchen countertop or a luxurious marble floor, Diamond Resin Dry Polishing Pads are your go-to solution.Another remarkable feature of these pads is their ability to perform effectively in dry polishing applications. Traditionally, wet polishing has been the preferred method due to its cooling effect, dust suppression, and easier debris removal. However, dry polishing offers its own set of advantages, such as convenience, versatility, and cost-effectiveness. Diamond Resin Dry Polishing Pads excel in this area, providing a superior dry polishing experience by delivering exceptional results without the need for water or slurry.Additionally, Diamond Resin Dry Polishing Pads offer enhanced flexibility and adaptability. Their design allows them to conform to the shape and contours of the surface being polished, ensuring even distribution of pressure and an immaculate finish. This makes them an ideal choice for intricate designs and curved surfaces, where achieving a perfect polish can be quite challenging.When it comes to achieving a high-gloss shine, Diamond Resin Dry Polishing Pads are second to none. The combination of diamond and resin creates a synergy that not only removes scratches and imperfections but also imparts a lustrous and reflective finish to the surface. This property is particularly significant in applications where aesthetics play a crucial role, such as luxury hotels, high-end residential properties, and commercial spaces.In terms of performance, Diamond Resin Dry Polishing Pads offer exceptional efficiency and endurance. The diamonds embedded in the pads ensure consistent cutting power, allowing for faster material removal and uniform polishing. This, coupled with their exceptional durability, makes them a cost-effective investment that can withstand rigorous use and produce superior results over an extended period.In conclusion, Diamond Resin Dry Polishing Pads have become a game-changer in the world of stone polishing. Their ability to polish various surfaces, adapt to different shapes, and deliver impeccable results without the need for water or slurry make them an essential tool for contractors and polishing professionals. Whether you are looking to enhance the beauty of your granite countertop, transform your marble floors, or revamp your terrazzo surfaces, Diamond Resin Dry Polishing Pads are your trusted companion. Invest in these pads and elevate your stone polishing projects to new heights of perfection.
Versatile Grinding Wheels for Industrial Metal Work and Deburring Applications
s, Bonded Grinding Wheels, Industrial Applications, Metal Work, Deburring, Bench Mounted Applications, Surface Grinding Wheels, Carbide BurrsGrinding Wheels and Tooling for Industrial ApplicationsGrinding wheels are essential tools for metalworking, deburring, and machine-mounted works. They come in various shapes and sizes and are known to be one of the most versatile abrasive tools available in the market. They are made of abrasive grains, bonding materials, and fillers, and can be used for a wide range of tasks. In this article, we will discuss the different types of grinding wheels and tooling for industrial applications.Bonded Grinding WheelsBonded grinding wheels are the most commonly used type of grinding wheel. They are made of a composite material that consists of abrasive grains held together by a bonding material. The abrasive grains are usually made of aluminum oxide, silicon carbide, or diamond, depending on the type of material being ground and the desired finish. The bonding material can be resin, metal, or vitrified.Resin-bonded wheels are commonly used for precision grinding, surface grinding, and tool and cutter grinding. They are versatile and affordable, making them suitable for most applications. Metal-bonded wheels are used for grinding harder materials, such as high-speed steel and carbide. They are also used for rough grinding and form grinding. Vitrified-bonded wheels are used for precision grinding and sharpening of carbide tools.Wire BrushesWire brushes are another type of abrasive tool that is used for cleaning, deburring, and finishing metal surfaces. They are made of metal wire bristles that are mounted on a rotating shaft. The wire bristles can be made of different materials, including steel, brass, and stainless steel. Wire brushes are used for removing rust, paint, and other surface contaminants from metal surfaces. They are also used for cleaning welds and deburring edges.Bench Mounted ApplicationsBench-mounted grinding wheels are used for precision grinding, sharpening, and polishing of metal parts. They are mounted on a bench or pedestal and can be used for a wide range of tasks, such as grinding, deburring, and sanding. Bench-mounted wheels are available in various sizes and materials, depending on the application.Surface Grinding WheelsSurface grinding wheels are used for precision grinding of flat surfaces. They are typically used on a reciprocating table, where the workpiece is moved back and forth against the grinding wheel. Surface grinding wheels are available in different sizes and materials, depending on the type of material being ground and the desired finish.Carbide BurrsCarbide burrs are used for shaping, deburring, and finishing metal surfaces. They are made of carbide, a hard and brittle material that is ideal for grinding and cutting. Carbide burrs are available in various shapes and sizes, depending on the application. They can be used on a variety of materials, including steel, aluminum, and cast iron.In conclusion, grinding wheels and tooling for industrial applications are essential tools for metalworking, deburring, and machine-mounted works. Bonded grinding wheels, wire brushes, bench-mounted applications, surface grinding wheels, and carbide burrs are just some of the available options. When choosing a grinding wheel or tool, it is important to consider the type of material being ground, the desired finish, and the application.
125mm Hook & Loop Backing Pad for Sanders & Polishers: Perfect Fit for 125mm Grinders, Polishers | M14 Thread For Hook and Loop Sanding Discs and Polishing Bonnets | Max12,250rpm
article discussing the benefits of using a 125mm Hook & Loop Backing Pad for sanders and polishers in various industries.The use of Hook & Loop Backing Pads has become increasingly popular in the sanding and polishing industries due to its versatility and ease of use. Backing pads make sanding and polishing tasks easier and more efficient by providing a stable surface for abrasive discs and polishing bonnets to attach to. The 125mm Hook & Loop Backing Pad is one such example that has caught the attention of professionals and DIY enthusiasts alike.Officially known as the ABS Backing Pad for Polisher, this 125mm Hook & Loop Backing Pad fits 125mm Grinders, Polishers, and can operate at a maximum speed of 12,250 RPMs. The M14 Thread for Hook and Loop Sanding Discs and Polishing Bonnets also ensures easy and secure attachment and detachment of sanding and polishing discs.According to industry experts, the 125mm Hook & Loop Backing Pad is one of the most versatile backing pads in the market. It can accommodate a wide range of sanding discs and polishing bonnets, making it suitable for use in various industries like automotive, woodworking, metalworking, and more. In the automotive industry, this backing pad is commonly used for polishing car surfaces, preparing paint surfaces, and sanding metal parts.In woodworking, the 125mm Hook & Loop Backing Pad is perfect for sanding wood surfaces. The Hook & Loop attachment allows for easy and quick change of sanding discs, ensuring that the woodworking process remains uninterrupted. With the added stability provided by the backing pad, sanding can be done with greater accuracy and precision, leading to smoother finishes.Metalworking is another industry where the 125mm Hook & Loop Backing Pad comes in handy. When used in conjunction with abrasive discs, it can quickly remove rust, paint, and other coatings from metal surfaces. The Hook & Loop attachment ensures that the abrasive discs remain attached to the backing pad during use, reducing the risk of accidents.Apart from its versatility, the 125mm Hook & Loop Backing Pad also offers several benefits to users. Its ABS material provides durability and prevents deformation during use, ensuring consistent performance throughout. The Hook & Loop attachment also makes it easy to change sanding and polishing discs, reducing downtime during the sanding and polishing process.Furthermore, the 125mm Hook & Loop Backing Pad ensures that abrasive discs and polishing bonnets remain firmly attached to the backing pad during use, preventing slippage and improving user safety. The maximum speed of 12,250 RPMs also ensures efficient sanding and polishing, saving precious time for professionals.In conclusion, the 125mm Hook & Loop Backing Pad is a versatile and efficient tool that offers numerous benefits to professionals and DIY enthusiasts. Its ability to accommodate a wide range of sanding discs and polishing bonnets, combined with its ease of use, durability, and safety features, makes it an indispensable tool for numerous industries. With its affordable price point, this backing pad is a great addition to any sanding and polishing toolkit.
High Quality Diamond Saw Blades for Granite - Order Online or Call Now
Diamond Tools For Granite: Enhancing Efficiency and Precision in CuttingIn the world of construction and home improvement, the importance of high-quality tools cannot be overstated. When it comes to cutting through the toughest materials, such as granite, using diamond tools is essential. With their exceptional durability, efficiency, and precision, diamond tools have become the go-to choice for professionals and DIY enthusiasts alike.Granite, with its unmatched beauty and strength, has become a popular choice for countertops, flooring, and other applications. However, working with such a dense and hard material requires specialized tools that can withstand the rigors of the task. This is where diamond tools for granite come into play.Diamond tools are renowned for their exceptional hardness and longevity. Unlike traditional metal blades, diamond tool blades are made with tiny industrial diamonds embedded in the cutting segment. These diamonds act as cutting edges, delivering incredible speed and precision while withstanding the abrasive nature of granite.One of the key advantages of diamond tools for granite is their ability to cut through the material quickly and effortlessly. The diamond blade's sharp cutting edges make clean and precise cuts, reducing the chances of chipping or cracking the granite. This not only saves time but also reduces material wastage during the cutting process, ultimately saving costs.Another significant advantage of diamond tools for granite is their exceptional durability. Granite is notorious for wearing down blades quickly due to its hardness. However, diamond blades are specifically designed to handle the toughest cutting tasks. The diamond particles on the cutting edge maintain their sharpness for an extended period, ensuring consistent performance throughout the project.Precision is critical when working with granite, as even the smallest errors can result in aesthetic flaws or compromised structural integrity. Diamond tools for granite offer unparalleled precision, enabling professionals to achieve the desired results with utmost accuracy. The sharp cutting edges of the diamond blades enable clean cuts, preventing any damage to the granite surface.Additionally, the use of diamond tools reduces the need for additional manual finishing work. Since diamond blades produce clean and smooth cuts, the granite surfaces require minimal polishing or shaping afterward. This not only saves time but also ensures a higher level of consistency in the final product.When choosing diamond tools for granite, it is essential to consider the specific requirements of your project. There are various types of diamond blades available, each designed for a specific cutting task. For instance, segmented blades are ideal for general cutting, while continuous rim blades are better suited for smooth cuts. Understanding the nuances of each blade type will help you make an informed decision and achieve the best results.In conclusion, diamond tools are the epitome of efficiency and precision when it comes to cutting granite. Their unparalleled durability, speed, and accuracy make them an indispensable asset for any professional or DIY enthusiast. By investing in high-quality diamond tools for granite, you can enhance your cutting capabilities, save time and money, and achieve impeccable results in your projects.Interested in acquiring diamond tools for your granite cutting needs? Order online or give us a call today at [phone number]. Our team of experts will assist you in choosing the right tools to take your granite cutting experience to the next level.
Rewrite for SEO optimization: Supplier for Wet Polishing Pads - Weihai Chengxun Import & Export Co., Ltd., offering a wide range of granite slabs, tombstones, granite countertops, vanity tops, monuments, slate and marble fireplaces, wooden shutters, film faced plywood, garden fountains, water pots, marble carvings, diamond tools, cutting blades, and polishing pads.
Diamond Wet Polishing Pads: The Ultimate Guide to Achieving Perfect Stone FinishPolishing is an important process in the production of stone surfaces. It is the final step that helps improve the aesthetic value of the stone. Because of the huge demand for stone products, manufacturers are always looking for ways to improve their production processes to ensure they deliver top-quality products. This has led to the production of different types of polishing pads. Diamond wet polishing pads are currently the most popular type of polishing pads on the market. In this article, we’ll take a closer look at diamond wet polishing pads.What are diamond wet polishing pads?Diamond wet polishing pads are polishing tools used to polish stone surfaces, such as granite, marble, and concrete. They are called "diamond" wet polishing pads because they are made of diamond particles. This means that they are designed to handle tougher materials, unlike traditional polishing pads. They are called "wet" polishing pads because they are used in combination with water. The water acts as a lubricant and helps to reduce heat generated during the polishing process.What makes diamond wet polishing pads unique?Diamond wet polishing pads are unique because they are designed to last longer than traditional polishing pads. This is because they are made of diamond particles, which are durable and wear-resistant. This allows them to handle even the toughest materials, providing a consistent and flawless finish. They are also the best choice when it comes to polishing edges and corners, as they provide excellent precision, and leave no scratches or marks.What are the different types of diamond wet polishing pads?There are different types of diamond wet polishing pads available on the market. They vary in terms of their size, quality, and intended use. Some popular types include:1. Electroplated diamond polishing pads: These are diamond pads that are attached to the backing plate with an electroplating process. They are durable and provide excellent results when polishing granite and other hard materials.2. Resin diamond polishing pads: These are diamond pads that use a resin binder to hold the diamond particles together. They are suitable for use on softer stones, such as marble or travertine.3. Metal bond diamond polishing pads: These are diamond pads that are designed to handle the toughest materials, such as concrete. They are the most aggressive type of diamond polishing pad and will leave scratches that can be removed by finer grits.How to use diamond wet polishing pads?Using diamond wet polishing pads is a fairly simple process. Here are some steps to follow:1. Choose the right pad grit: Depending on the type of stone you are polishing, you will need to choose the correct grit. Start with a coarser grit and work your way up to finer grits until you achieve the desired finish.2. Attach the pad: Attach the diamond pad to a polisher. Ensure that the polisher is water-fed to keep the surface of the stone cool and to avoid dust.3. Begin polishing: Start polishing the surface of the stone, moving the polisher in a circular motion. Keep the surface wet at all times to prevent overheating.4. Change the pads: As you move from coarser to finer grits, change to a new pad. This is to avoid cross-contamination and to achieve the desired finish.ConclusionDiamond wet polishing pads are a must-have for anyone looking to achieve a perfect, polished finish on stone surfaces. They are durable and long-lasting, providing a consistent finish every time. With the right technique and grit sequence, you can achieve an excellent finish on any stone material. Make sure to always choose the right grit for the stone you are working on, and to keep the surface wet to avoid overheating. With diamond wet polishing pads, you can achieve a stunning, polished finish that will last for years to come.